Porcelana kostna jest słusznie uważana za „królewską” - cienką, śnieżnobiałą, dzwoniącą, półprzezroczystą … Jedyną fabryką w Rosji, która produkuje takie naczynia, jest Imperialna Fabryka Porcelany. Jak iz czego powstaje taka porcelana i dlaczego nazywa się ją porcelaną kostną?
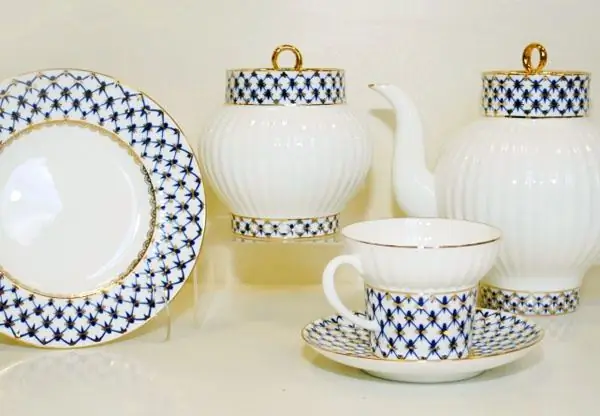
Porcelana „na kościach”: produkt niedoboru
Słowo „kość” w nazwie najlepszej porcelany nie jest metaforą, ale dosłownym wskazaniem składu surowca. Zwykła masa porcelanowa składa się z kaolinu - białej gliny i innych materiałów glinianych, które po wypaleniu nadają biały kolor, a także kwarcu i skalenia. W Anglii w połowie XVIII wieku zaczęto dodawać do kompozycji popiół kostny - zawarty w nim fosforan wapnia nadawał potrawom tak niesamowitą biel.
W Cesarskiej Fabryce Porcelany (w czasach sowieckich nazywano ją Łomonosow) w latach sześćdziesiątych XX wieku zaczęto produkować porcelanę kostną. To paradoksalne, ale prawdziwe: powodem, dla którego zakład opanował tę technologię, nie było ambitne pragnienie produkcji elitarnych „królewskich” potraw, ale… brak surowców.
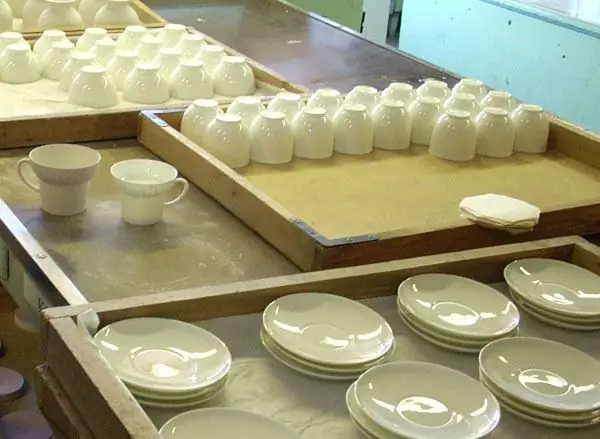
Od 1965 roku zakład przeżywał poważne trudności z zaopatrzeniem w kaolin - biała glinka była bardzo szeroko stosowana w przemyśle papierniczym, perfumeryjnym i wojskowym. Ale w kraju było dużo odpadów kostnych. Dlatego dyrektor zakładu Aleksander Siergiejewicz Sokołow postawił przed laboratorium produkcyjnym LFZ zadanie: opracować skład masy do porcelany kostnej.
Skład surowców został dobrany metodą prób i błędów (zagraniczni koledzy nie spieszyli się z ujawnianiem tajemnic handlowych). W efekcie okazało się na przykład, że ptasie kości nadawały porcelanie zbędny liliowy odcień.
W rezultacie osiedliliśmy się na piszczelu bydła. Ponadto nie brakowało surowców. Produkcja guzików wybitych z odtłuszczonych kości guzików do poszewek na poduszki i do mundurów wojskowych - a odpady trafiały do fabryki porcelany, gdzie były spalane.
Masa do wyrobu porcelany kostnej składała się tylko w 55% z tradycyjnego kaolinu, gliny, skalenia i kwarcu - resztę stanowił popiół kostny.
W 1968 roku w zakładzie uruchomiono warsztat porcelany kostnej. W przeciwieństwie do porcelany angielskiej, która była dość gruba, LFZ zdecydowało się na produkcję porcelany cienkościennej. I na początku nawet „przesadzili”: pierwsze kubki okazały się tak cienkie i nierealistycznie lekkie, że klienci zaczęli narzekać na poczucie „plastyczności”. Dlatego zdecydowano się zwiększyć grubość odłamka o 0,3 mm.
Narodziny „cienkich rzeczy”
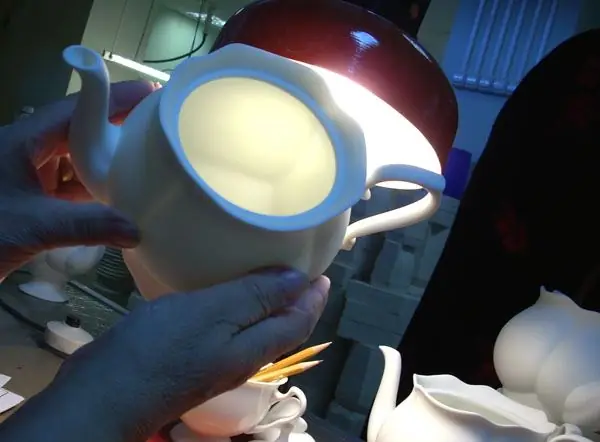
Kubki z porcelany kostnej, podobnie jak wiele innych wyrobów porcelanowych, są wykonywane metodą odlewania. W tym celu formy odlane z gipsu wypełnia się po brzegi płynną mieszanką porcelany przypominającą śmietanę - poślizg. Gips zaczyna „odbierać” wilgoć z poślizgu - w wyniku czego na wewnętrznych ściankach formy stopniowo narasta porcelanowa „skorupa”. Gdy osiągnie wymaganą grubość, nadmiar poślizgu jest usuwany z formy. Następnie wysuszony „garnek” (jak nazywa się niewypaloną porcelanę) zaczyna pozostawać w tyle za ściankami formy - i jest usuwany.
W produkcji figurek porcelanowych części „nabierają grubości” przez dość długi czas - kilka godzin. W przypadku cienkościennych kubków wszystko dzieje się znacznie szybciej - w Imperial Porcelain Factory mieszanka porcelany kostnej jest wlewana do foremek tylko przez dwie minuty.
Oliwka jest automatyczna - formy poruszają się po okręgu, wymagana ilość poślizgu jest automatycznie wylewana z dozownika, a następnie podciśnienie „zabiera” nadmiar.
Uchwyty na filiżanki, czajniczki, cukiernice odlewane są osobno, a następnie „sklejane” ręcznie. Ta sama mieszanka porcelany działa jak klej, tylko grubszy.
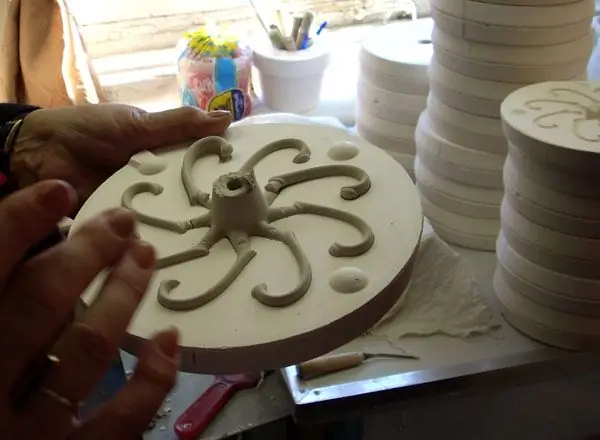
Wyroby płaskie (spodki, talerze) wykonywane są metodą tłoczenia. Półprodukt porcelanowy do takich produktów jest bardzo gęsty, przypomina plastikowe ciasto zwinięte w „kiełbasy”. Odcięty kawałek „kiełbasy” umieszcza się na formie gipsowej, a od góry opuszcza się na nią obracający się wałek formujący (każdy model ma własny wałek). Nadmiar odcinany jest automatycznie, ale oszlifowanie krawędzi i spłaszczenie powierzchni to zadanie tzw. „ramek”, pracujących wyłącznie ręcznie.
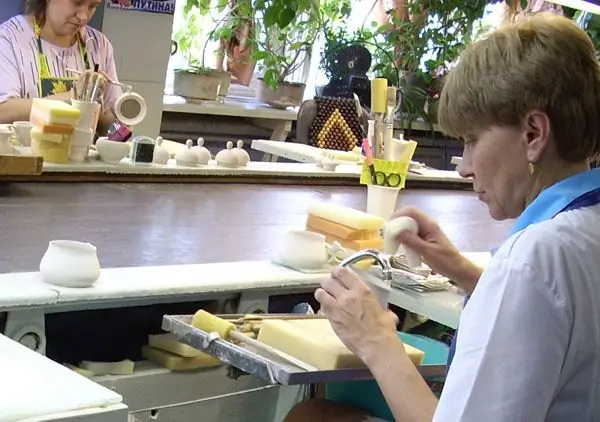
Gąbka, pędzel, matowe szkło, papier ścierny - narzędzia używane przy oprawkach są proste, ale skuteczne i sprawdzone w czasie. Porcelanowe główki trafiają do nich po wyschnięciu.
Jak odłamek jest hartowany
Porcelana kostna jest wypalana dwukrotnie. Ponadto temperatura pierwszego wypalania jest bardzo wysoka - 1250 - 1280 stopni, czyli znacznie wyższa niż w przypadku zwykłej porcelany. W tej temperaturze mieszanka porcelany jest całkowicie „upieczona” i uzyskuje niezbędną wytrzymałość. Naczynia spędzają w piekarniku 12 godzin. A tak przy okazji, zmniejsza się o około 13%.
Ale jeszcze nie świeci. Brokat pojawi się po glazurowaniu porcelany. Składa się z tych samych materiałów co porcelana, tylko w różnym procencie, dodatkowo dodaje się do niego marmur i dolomit. Podczas wypalania glazura topi się, tworząc błyszczącą błyszczącą powierzchnię.
Szkliwo nakłada się na porcelanę kostną za pomocą pistoletu natryskowego - najpierw z jednej strony, a następnie z drugiej strony. Abyś mógł kontrolować gęstość i grubość warstwy, szkliwo jest zabarwione na kolor magenta. Dlatego, idąc do pieca na ostateczne wypalenie, filiżanki i spodki mają jasny liliowy kolor. W wysokich temperaturach pigment wypala się, a porcelana staje się biała.
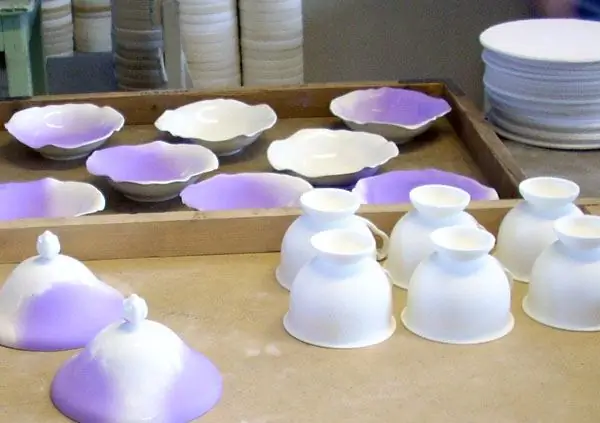
Drugie wypalanie również trwa 12 godzin, tylko temperatura tym razem jest nieco niższa - 1050-1150 °C.
Nawiasem mówiąc, to właśnie temperatura wypalania porcelany kostnej stała się powodem, dla którego Fabryka Porcelany Łomonosowa zdołała utrzymać monopol na produkcję rosyjskiej porcelany kostnej.
W sowieckich fabrykach nie było zwyczaju utrzymywania technologii w tajemnicy, dlatego na początku lat 70. projekty technologii i wyposażenia zostały „przedstawione” Republice Bułgarskiej, gdzie w tym czasie uruchomiono nową produkcję porcelany. W 1982 roku technologia została przeniesiona do fabryki ceramiki w Kownie na Litwie. Ale rosyjskie fabryki nie odważyły się podjąć produkcji porcelany kostnej. Haczyk okazał się taki, że taka porcelana jest bardzo wrażliwa na temperaturę wypalania - a odchylenie od ustawionych parametrów temperatury dosłownie o 10 stopni zamienia naczynia w złom. Jednocześnie, jeśli chodzi o temperatury powyżej tysiąca stopni, nawet błąd przyrządów pomiarowych może przekroczyć te same 10 stopni. LFZ pozostała więc jedynym producentem „królewskiej porcelany” w całym kraju.
Jak pojawia się wzór?
Czysta biała, niepomalowana porcelana, której nie dotykała ręka artysty, eksperci nazywają „lenem”. Ale zanim trafią na lady sklepów firmowych, naczynia muszą być ozdobione wzorem.
Malowanie na porcelanie może być podszkliwne, nałożone i połączone, łącząc obie te techniki. W takich przypadkach rysunek jest nakładany dwuetapowo. Przykładem malarstwa kombinowanego jest słynny wzór „Kobaltowa sieć”, który stał się rodzajem „wizytówki” rośliny.
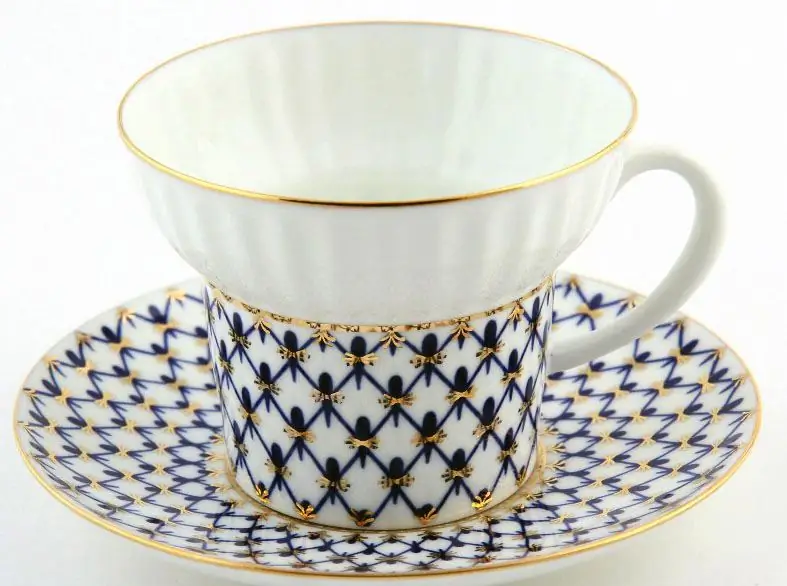
Wzór kobaltu - niebieskie linie - jest nakładany na porcelanę jeszcze przed nałożeniem glazury - podczas wypalania w wysokiej temperaturze dekor jest "wtapiany" w przezroczystą glazurę. Kobalt, który przed wypaleniem ma matowy, wyblakły czarny kolor, po podgrzaniu magicznie zmienia się i w zależności od stężenia, wzór staje się bladoniebieski lub ciemnoniebieski. Nawiasem mówiąc, wszystkie farby stosowane w malowaniu podszkliwnym zachowują się w ten sam sposób - ich kolor "pojawia się" podczas ekspozycji na temperaturę, a podczas rysowania obrazu wyglądają na wyblakłe - odcienie czerni, szarości, brązu. A artyści, którzy pracują z kilkoma kolorami jednocześnie, mają trudności: stale muszą „pamiętać” o przyszłym obrazie.
Rysunek często jest nakładany ręcznie, ale czasami praca ta może być łatwiejsza. Na przykład w Cesarskiej Fabryce Porcelany opracowali specjalne formy do naczyń, które będą ozdobione „kobaltową siatką”: cienkie, ledwo zauważalne rowki są „narysowane” po bokach odłamka - rodzaj konturu, który należy ręcznie „zarysowane” liniami kobaltu.
Kobaltowy wzór można również nanieść na produkt za pomocą kalkomanii - cienkiej folii przypominającej kalkomanię, na której nadrukowany jest kobaltowy wzór.
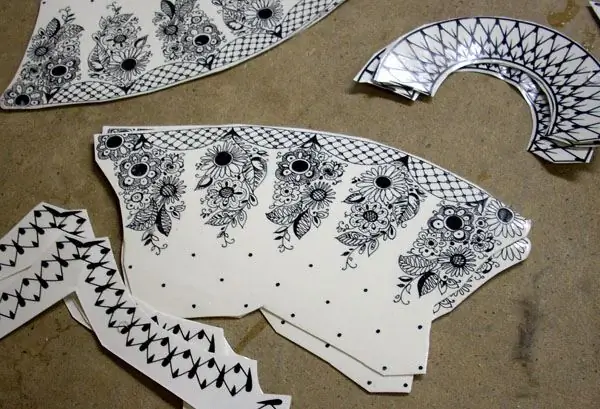
Kształt kalkomanii dokładnie pasuje do kształtu naczyń - jest inny dla każdego modelu. Po podgrzaniu folia wypala się, a wzór jest odciskany na powierzchni produktu.
Wzór podszkliwny jest nakładany po przejściu produktów przez pierwsze wypalanie - a przed glazurowaniem. Po drugim wypaleniu takie naczynia czasami wyglądają bardzo dziwnie - pierwsza część obrazu została już na nią nałożona, a druga wciąż czeka na skrzydłach. Ale już możesz sobie wyobrazić, jak to będzie wyglądać.
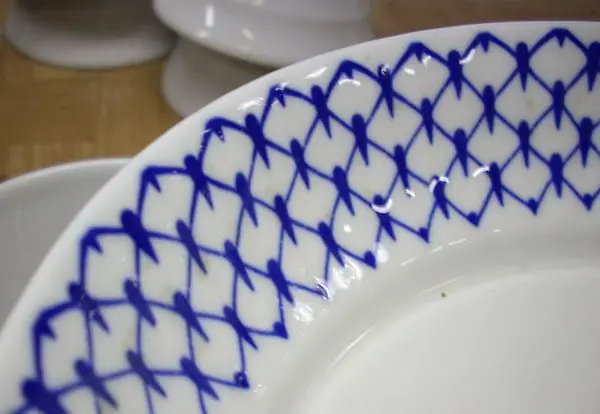
Malowanie złotem to już malowanie przez glazurę. Następnie naczynia przejdą kolejne wypalanie, ale w niższych temperaturach - tylko w celu utrwalenia wzoru. Dzięki temu do malowania można używać metali szlachetnych, a także wielu farb, które nie wytrzymują „czterocyfrowych” temperatur. Złote gwiazdki można nanieść na firmowy design ręcznie, pędzlem lub za pomocą miniaturowej pieczątki.